Cải tiến trong sản xuất tại công ty Hồng Bàng
Cải tiến trong sản xuất tại sản xuất nhà máy thực phẩm chức năng công ty Hồng Bàng là một trong những yếu tố để tăng suất lao động. Trải qua 2 năm phát động phong trào Kaizen, chúng tôi nhận thấy rằng: Có rất nhiều ý tưởng Kaizen được đưa ra với tiêu chí “thay đổi để tốt hơn” nhưng cái TỐT HƠN thực sự ấy là bao nhiêu, tốt hơn như thế nào thì lại không thể biết được. Và sau nhiều ngày băn khoăn trăn trở, chúng tôi chợt phát hiện ra rằng: mình đưa ra ý tưởng nhưng lại không biết xuất phát từ đâu. Sự vô lý này khiến chúng tôi bắt đầu một hành trình cải tiến mới.
Cải tiến trong sản xuất khởi nguồn từ lãng phí
Là một đơn vị chuyên nghiên cứu, sản xuất thực phẩm chức năng và các sản phẩm hóa mỹ phẩm, yếu tố sống còn chính là NĂNG SUẤT. Tại Hồng Bàng, chúng tôi nhận thấy rằng: Có những ý tưởng cải tiến trong sản xuất đưa ra đúng là có tốt hơn nhưng lại chẳng mang lại hiệu quả gì về mặt thời gian cả – và đồng nghĩa là không thể cải thiện được năng suất. Từ đó, chúng tôi cũng nhận thấy rằng, cải tiến buộc phải loại bỏ được lãng phí (trong đó lãng phí thời gian là lãng phí được ưu tiên giải quyết).
Chúng tôi đã tìm hiểu rất kỹ về 7 loại lãng phí trong sản xuất và bắt đầu công cuộc TÌM bằng được lãng phí trong nhà xưởng công ty Hồng Bàng.
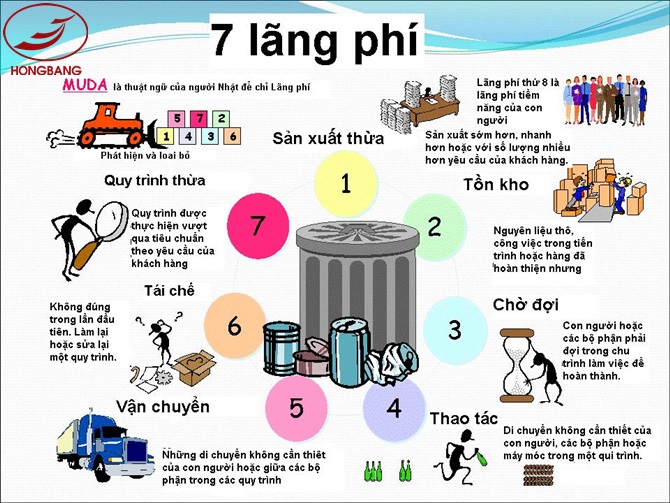
7 loại lãng phí trong sản xuất
Làm thế nào để biết có lãng phí
Nhà máy đã lập một đoàn khảo sát lãng phí. Đoàn khảo sát của nhà máy đã chỉ ra một số điểm lãng phí tương ứng với 7 loại lãng phí kể trên. Những lãng phí về thời gian và di chuyển là những lãng phí dễ nhận thấy nhất và tất cả mọi người đều nhất trí nó là LÃNG PHÍ. Điều này rất quan trọng, vì chỉ khi tất cả cùng nhận thấy lãng phí thì tinh thần cải tiến mới thực sự bộc lộ.
Một trong số những lãng phí điển hình được đoàn khảo sát ghi lại đó là:
Trong công đoạn bao phim viên nén thực phẩm chức năng, có bước đóng túi viên sau bao phim. Hiện tại viên từ phòng bao phim được chuyển đến phòng đóng túi phải đi qua 2 hành lang có chiều dài khoảng 15m (cụ thể trong hình) và lại phải vòng trở lại vị trí cũ để chuyển bán thành phẩm ra ngoài phòng đóng gói. Hoạt động này phát sinh thường xuyên (khoảng 6 lần/ ngày). Đoàn khảo sát và tổ sản xuất sau khi xem xét thực tế thì nhận thấy đây là điểm lãng phí rất đáng kể.
Không phải lãng phí nào cũng lao vào cải tiến
Rõ ràng, không phải cứ uống nước và hít không khí là chúng ta có thể bắt tay vào cải tiến. Có những cải tiến trong sản xuất bắt buộc phải đầu tư – phải cân nhắc lợi ích giữa việc đầu tư và hiệu quả thu lại do cải tiến. Có những cải tiến trong sản xuất không phải đầu tư, nhưng việc thực hiện nó lại khiến chúng ta thay đổi quá nhiều hoạt động khác – cũng cần phải cân nhắc. Và vì thế, trong số những lãng phí được chỉ ra trong đợt khảo sát, chúng tôi lựa chọn lãng phí di chuyển để tập trung biện pháp. Quả thật, khi tập trung vào nó, biện pháp chợt đến thật nhẹ nhàng.
Bằng việc thay đổi vị trí phòng đóng túi viên sau xử lý vi sinh, quãng đường di chuyển bán thành phẩm từ phòng bao phim 1 đã giảm từ 13 còn 3m (giảm 10/ lần di chuyển), từ phòng bao phim 2 giảm từ 18m còn 2m (giảm 16m// lần di chuyển) – trung bình là 13m/ lần di chuyển.
Với hoạt động thường xuyên của công đoạn bao phim, nhà máy đã tiết kiệm được: 13m x 6 lần di chuyển mỗi ngày x 24 ngày = 1.872m di chuyển/ tháng
Quãng đường di chuyển tiết kiệm được tuy không phải là quá lớn nhưng kèm theo đó là việc tiết kiệm phương tiện vận chuyển (xe đẩy), thời gian di chuyển của người, thời gian thực hiện công việc… Và hơn cả, đó là việc khích lệ tinh thần của tất cả mọi người vì hiệu quả rõ ràng và rất thực tế do cải tiến đem lại.
Cải tiến trong sản xuất
Đối với nhà máy sản xuất nói chung và nhà máy sản xuất thực phẩm chức năng của Hồng Bàng nói riêng, thực hiện cải tiến trong sản xuất không thể như phong trào. Nó cần là một hoạt động hiệu quả, bền vững. Điều này không hề khó: Chỉ cần cải tiến trong sản xuất đúng vào điểm lãng phí và tính toán được hiệu quả do cải tiến mang lại.